Material Selection: The Foundation of Pressure Resistance
Material selection stands as a pivotal factor determining the pressure resistance of internal combustion engine fuel injection high-pressure pipes. Traditionally, metallic materials like stainless steel and aluminum alloys have been widely employed in the manufacturing of high-pressure pipes. These materials possess high mechanical strength and corrosion resistance, enabling them to withstand substantial pressures. In recent years, the emergence of novel materials such as carbon fiber-reinforced composites has further enhanced the pressure resistance capabilities of high-pressure pipes. Carbon fiber-reinforced composites exhibit exceptional strength-to-weight ratio and stiffness, allowing them to withstand higher pressures with smaller cross-sectional dimensions. This enables high-pressure pipes to achieve lightweighting while maintaining strength.
Manufacturing Processes: Shaping Pressure Resistance
Manufacturing processes also play a significant role in influencing the pressure resistance of high-pressure pipes. Conventional manufacturing techniques include cold drawing, cold extrusion, and forging. These processes enhance the strength and density of the material but have limitations in achieving higher pressure resistance. The advent of advanced manufacturing technologies like laser welding, numerical control (NC) machining, and precision forming has revolutionized the manufacturing of high-pressure pipes. Laser welding technology enables high-strength welded joints, ensuring the sealing and pressure resistance of the high-pressure pipes. NC machining and precision forming techniques, on the other hand, improve the surface quality and dimensional accuracy of high-pressure pipes, further enhancing their pressure resistance.
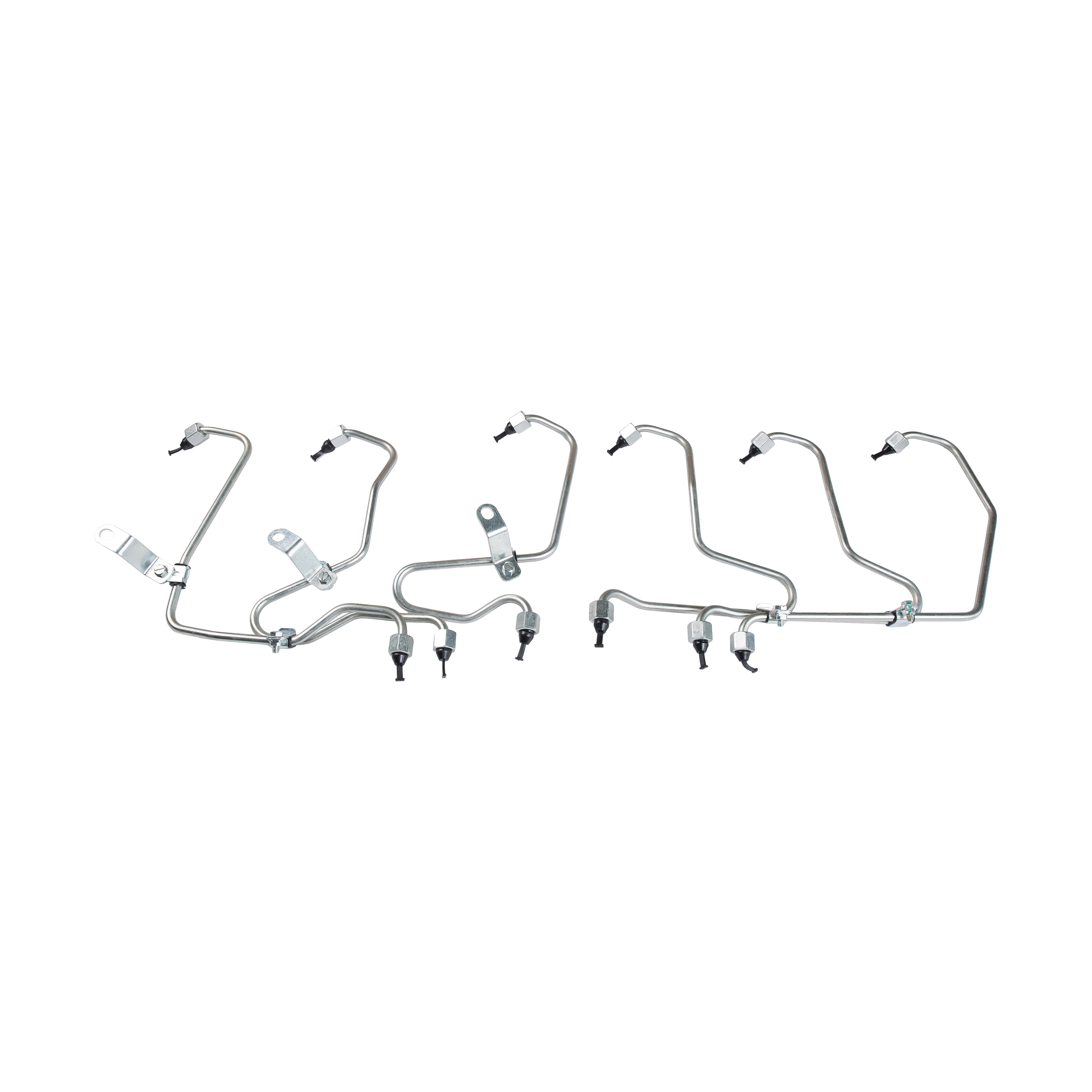
Future Outlook: Advancing Pressure Resistance for Automotive Excellence
As the automotive industry's demands for performance, safety, and environmental friendliness continue to rise, the superior pressure resistance of internal combustion engine fuel injection high-pressure pipes will become a critical factor limiting their development. Therefore, material research and manufacturing process optimization will be the focal points for future high-pressure pipe development. With continuous innovation in materials science and manufacturing technologies, it is anticipated that new materials and manufacturing processes will emerge, offering more possibilities for enhancing the pressure resistance of internal combustion engine fuel injection high-pressure pipes, thereby driving the progress and development of the automotive industry.
The Enduring Significance of Pressure Resistance
The exceptional pressure resistance of internal combustion engine fuel injection high-pressure pipes is a crucial safeguard for their stable operation. Material selection and manufacturing processes are the key factors influencing the pressure resistance of high-pressure pipes. With the continuous advancement of materials science and manufacturing technologies, the pressure resistance of high-pressure pipes will continue to improve, providing a more solid foundation for the development of the automotive industry.